Predictive Maintenance in Automotive Manufacturing
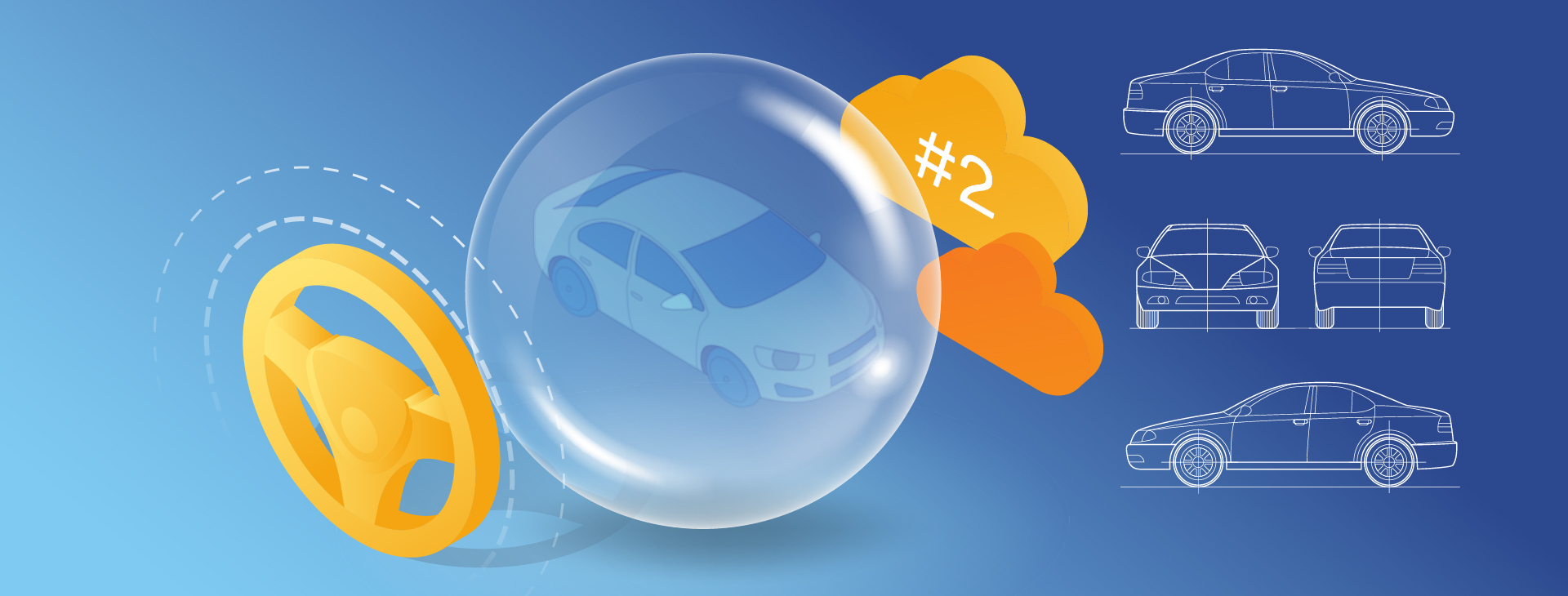
Our initial article on predictive maintenance covered the definition of such a system, its construction, and the key implementation challenges. In this part, we’ll delve into how PdM technology is transforming different facets of the automotive industry and its advantages for OEMs, insurers, car rental companies, and vehicle owners.
Best predictive maintenance techniques and where you can use them
In the first part of the article, we discussed the importance of sensors in a PdM system. These sensors are responsible for collecting data from machines and vehicles, and they can measure various variables like temperature, vibration, pressure, or noise. Proper placement of these sensors on the machines and connecting them to IoT solutions, enables the transfer of data to the central repository of the system. After processing the data, we obtain information about specific machines or their parts that are prone to damage or downtime.
The automotive industry can benefit greatly from implementing these top predictive maintenance techniques.
Vibration Analysis
How does it work?
Machinery used in the automotive industry and car components have a specific frequency of vibration. Deviations from this standard pattern can indicate “fatigue” of the material or interference from a third-party component that may affect the machine’s operation. The PdM system enables you to detect these anomalies and alert the machine user before a failure occurs.
What can be detected?
The technique is mainly applied to high-speed rotating equipment. Vibration and oscillation analysis can detect issues such as bent shafts, loose mechanical components, engine problems, misalignment, and worn bearings or shafts.
Infrared Thermography Analysis
How does it work?
The technique involves using infrared cameras to detect thermal anomalies. This technology can identify malfunctioning electrical circuits, sensors or components that are emitting excessive heat due to overheating or operating at increased speeds. With this advanced technology, it’s possible to anticipate and prevent such faults, and even create heat maps that can be used in predictive models and maintenance of heating systems.
What can be detected?
Infrared analysis is a versatile and non-invasive method that can be used on a wide scale. It is suitable for individual components, parts, and entire industrial facilities, and can detect rust, delamination, wear, or heat loss on various types of equipment.
Acoustic Analysis Monitoring
How does it work?
Machines produce sound waves while operating, and these waves can indicate equipment failure or an approaching critical point. The amplitude and character of these waves are specific to each machine. Even if the sound is too quiet for humans to hear in the initial phase of malfunction, sensors can detect abnormalities and predict when a failure is likely to occur.
What can be detected?
This PdM technology is relatively cheaper compared to others, but it does have some limitations in terms of usage. It is widely used in the Gas & Oil industry to detect gas and liquid leaks. In the automotive industry, it is commonly used for detecting vacuum leaks, unwanted friction, and stress on machine parts.
Motor Circuit Analysis
How does it work?
The technique works through electronic signature analysis (ESA). It involves measuring the supply voltage and operating current of an electronic engine. It allows locating and identifying problems related to the operation of electric engine components.
What can be detected?
Motor circuit analysis is a powerful tool that helps identify issues related to various components, such as bearings, rotor, clutch, stator winding, or system load irregularities. The main advantage of this technique is its short testing time and convenience for the operator, as it can be carried out in just two minutes while the machine is running.
PdM Oil Analysis
How does it work?
An effective method for Predictive Maintenance is to analyze oil samples from equipment without causing any damage. By analyzing the viscosity and size of the sample, along with detecting the presence or absence of third substances such as water, metals, acids or bases, we can obtain valuable information about mechanical damage, erosion or overheating of specific parts.
What can be detected?
Detecting anomalies early is crucial for hydraulic systems that consist of rotating and lubricating parts, such as pistons in a vehicle engine. By identifying issues promptly, effective solutions can be developed and potential damage to the equipment or a failure can be prevented.
Computer Vision
How does it work?
Computer vision is revolutionizing the automotive industry by leveraging AI-based technology to enhance predictive maintenance processes. It achieves this by analyzing vast datasets, including real-time sensor data and historical performance records, to rapidly predict equipment wear and tear. By identifying patterns, detecting anomalies, and issuing early warnings for potential equipment issues, computer vision enables proactive maintenance scheduling.
What can be detected?
In the automotive industry, computer vision technology plays a crucial role in detecting equipment wear and tear patterns to predict maintenance requirements. It can also identify manufacturing defects such as scratches or flaws, welding defects in automotive components, part dimensions and volumes to ensure quality control, surface defects related to painting, tire patterns to match with wheels, and objects for robotic guidance and automation.
Who and how can benefit from predictive maintenance
Smart maintenance systems analyze multiple variables and provide a comprehensive overview, which can benefit several stakeholders in the automotive industry. These stakeholders range from vehicle manufacturing factories and the supply chain to service and dealerships, rental companies, insurance companies, and drivers.
Below, we have outlined the primary benefits that these stakeholders can enjoy. In the OEMs section, we have provided examples of specific implementations and case studies from the market.
Car rentals
Fleet health monitoring and better prediction of the service time
Managing service and repairs for a large number of vehicles can be costly and time-consuming for rental companies. When vehicles break down or are out of service while in the possession of customers, it can negatively impact the company’s revenue. To prevent this, car rental companies need constant insight into the condition of their vehicles and the ability to predict necessary maintenance. This allows them to manage their service plan more efficiently and minimize the risk of vehicle failure while on the road.
Car dealerships
Reducing breakdown scenarios
Car dealerships use predictive maintenance primarily to anticipate mechanical issues before they develop into serious problems. This approach helps in ensuring that vehicles sold or serviced by them are in optimal condition, which aids in preventing breakdowns or major faults for the customer down the line. By analyzing data from the vehicle’s onboard sensors and historical maintenance records, dealerships can identify patterns that signify potential future failures. Predictive maintenance also benefits dealerships by allowing for proactive communication with vehicle owners, reducing breakdown scenarios, and enhancing customer satisfaction
Vehicle owners
Peace of mind
Periodic maintenance recommendations for vehicles are traditionally based on analyzing historical data from a large population of vehicle owners. However, each vehicle is used differently and could benefit from a tailored maintenance approach. Vehicles with high mileage or heavy usage should undergo more frequent oil changes than those that are used less frequently. By monitoring the actual vehicle condition and wear, owners can ensure that their vehicles are always at 100% and can better manage and plan for maintenance expenses.
Insurance companies
Risk & fraud
By using data from smart maintenance systems, insurance companies can enhance their risk modeling. The analysis of this data allows insurers to identify the assets that are at higher risk of requiring maintenance or replacement and adjust their premiums accordingly. In addition, smart maintenance systems can detect any instances of tampering with the equipment or negligence in maintenance. This can aid insurers in recognizing fraudulent claims.
OEMs successful development of PdM systems
BMW Group Case Study
The German brand implements various predictive maintenance tools and technologies, such as sensors, data analytics, and artificial intelligence, to prevent production downtime, promote sustainability, and ensure efficient resource utilization in its global manufacturing network. These innovative, cloud-based solutions are playing a vital role in enhancing their manufacturing processes and improving overall productivity.
The BMW Group’s approach involves:
- Forecasting phenomena and anomalies using a cloud-based platform. Individual software modules within the platform can be easily switched on and off if necessary to instantly adapt to changing requirements. The high degree of standardization between individual components allows the system to be globally accessible. Moreover, it is highly scalable and allows new application scenarios to be easily implemented.
- Optimizing component replacements (this uses advanced real-time data analytics).
- Carrying out maintenance and service work in line with the requirements of the actual status of the system.
- Anomaly detection using advanced AI predictive algorithms.
Meanwhile, it should be taken into account that in BMW’s body and paint shop alone, welding guns perform some 15,000 spot welds per day. At the BMW Group’s plant in Regensburg, the conveyor systems’ control units run 24/7. So any downtime is a huge loss.
→ SOURCE case study.
FORD Case Study
Predictive vehicle maintenance is one of the benefits offered to drivers and automotive service providers as part of Ford’s partnerships with CARUSO and HIGH MOBILITY. In late 2020, Ford announced two new connected car agreements to potentially enable vehicle owners to benefit from a personalized third-party offer.
CARUSO and HIGH MOBILITY will function as an online data platform that is completely independent of Ford and allows third-party service providers secure and compliant access to vehicle-generated data. This access will, in turn, enable third-party providers to create personalized services for Ford vehicle owners. This will enable drivers to benefit from smarter insurance, technical maintenance and roadside recovery.
Sharing vehicle data (warning codes, GPS location, etc.) via an open platform is expected to be a way to maintain competitiveness in the connected mobility market.
→ SOURCE case study.
Predictive maintenance is the future of the automotive market
An effective PdM system means less time spent on equipment maintenance, saving on spare parts, eliminating unplanned downtime and improved management of company resources. And with that comes more efficient production and customers’ and employees’ satisfaction.
As the data shows, organizations that have implemented a PdM system report an average decrease of 55% in unplanned equipment failures. Another upside is that, compared to other connected car systems (such as infotainment systems), PdM is relatively easy to monetize. Data here can remain anonymous, and all parties involved in the production and operation of the vehicle reap the benefits.
Organizations have come to recognize the hefty returns on investment provided by predictive maintenance solutions and have thus adopted it on a global scale. According to Market Research Future, the global Predictive Maintenance market is projected to grow to 111.30 billion by 2030, suggesting that further growth is possible in the future.
Check related articles
Read our blog and stay informed about the industry's latest trends and solutions.
see all articles